Keynote Speaker----Dr. Oleksandr Khotsianovskyi
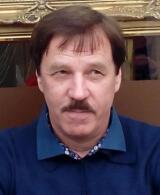
Dr. Oleksandr Khotsianovskyi, National Academy of Sciences of Ukraine, Pisarenko Institute of Strength of Materials, Kiev, Ukraine
Dr. Oleksandr Khotsianovskyi is currently a senior research fellow at the Institute of Problems of Strength (IPS), Kiev, Ukraine. After receiving the Ph.D. degree in Mechanical Engineering and Fracture Mechanics at the National Academy of Sciences of Ukraine in 1990, he conducted research in the field of innovative spacecraft and aircraft applications in IPS, Ukraine, as an invited research fellow in German Aerospace Research Establishment (DLR, Cologne,Germany,1993-1995), and Computer Control Solutions (CCS, Dublin, Ireland, 2001-2002). In 1996-2000, he was hired by USAID as a full-time technical consultant to six technical assistance projects financed by the USAID with the total budget of 5 mln USD in four CIS countries, including Ukraine (Kiev and ten more pilot cities), Russia (Irkutsk), Moldova (Cisinau) and Kazakhstan (Alma-Aty). His current research interests cover a wide range: from coatings, tribology, and fretting-fatigue of advanced space/aircraft materials to polymer-additive applications and numerical simulation of hydroelasticity problems for supercavitation high-speed underwater vehicles. He takes an active part in the advanced material development for spacecraft applications in Ukraine (IPS, Kiev) and ONR/DARPA international projects on drag reduction of superspeed underwater vehicles (2014-2017). He is the managing editor of the international journal Strength of Materials (Springer, US), guest editor in IOP Conference Series and other International Journals indexed in different databases. In the last five years, he participated as keynote speaker in four Global conferences on Materials Science and Engineering (CMSE2013, 2014, 2015, 2017) and one Global Conference on Polymer and Composite Materials (PCM 2016) in China.
Speech Title: Breakthrough Similarities of Cracks and Supercavities: Fretting Fatigue Crack and Supercavity Motion Progress Report
Abstract: We will discuss two phenomena occurring under oscillating shear and negative normal stress conditions: (i) fretting fatigue crack fast propagation in aircraft and spacecraft materials and (ii) ventilated super cavity formation and evolution around an underwater body (torpedo or projectile), which ensures it high-speed motion. A brief survey of the current development in this domain is supplemented by the author contributions to solving both problems via fracture and continuum mechanics.
Fretting fatigue is known to occur at relative displacement (slip) of a cyclically loaded structural component and a clamped counter body. Normal and shear surface stresses in slip give rise to early nucleation and quick propagation of short cracks with the stress intensity factors (SIF), being inversely proportional to the crack length, while the bulk SIF is directly proportional to it. Fracture mechanics approach is widely used for prediction of fretting fatigue propagation phase, corresponding to the larger share of the structural component total life. Mixed-Mode (KI and KII) initial crack propagation, dependent on the friction coefficient, is shown to be the most accurately predicted by the two-parameter criterion proposed by Otsuka and refined by the author. Since a particular combination of surface and bulk stresses controls the crack propagation direction and its rate, inducing the recurrent variation of the stress ratio R, this variation is accounted for via the Elber-Marci effective SIF concept modified by the author, while the effect of negative residual stresses, induced by shot- and laser peening, on SIF and total life is simulated. Fretting fatigue life calculation results are obtained or specimens and structural components from steels, aluminum and titanium alloys. The latest works and experimental techniques in this domain are briefly discussed, which combine the fracture mechanics and tribological techniques and provide the engineering approach that may be extended to other domains of solid body and fluid mechanics.
One of such domains is the supercavitating motion of underwater bodies at superhigh speeds. The in-water motion speed of modern surface vessels is limited by viscous resistance (drag) of water, which grows with the motion speed. A drastic drag reduction is achieved by separating the vessel hull from water using a disk- or cone-shaped cavitator, which “opens an umbrella” over the major part of the hull to produce an ellipsoidal air bubble (supercavity) inflated by an artificial or natural air inflow that makes possible a very high motion speed. This supercavitating principle was implemented in high-speed underwater vehicles (HSUV) and small water plane area twin hull (SWATH) vessels, as well as in famous Shkval high-speed torpedo, which appeared in USSR in 1977, i.e. about 40 years ago. However, a progress in this domain exhibited a saturation until 2005, when Barracuda supercavitating torpedo appeared in Germany. Then, in 2015, Chinese scientists managed to control the cavitation flow by supplying the aqueous solutions of high-molecular linear-chain polymers, which form a "liquid membrane" around an underwater vehicle and ensure its stable in-water ultrasonic motion. Some noteworthy results were also obtained in the last two years by a team of Ukrainian scientists including the author within a framework of the US (DAPRA/ONR) project. Those include experimental study of supercavitating flows past a conic cavitator at nonzero angle of attack, in particular, underwater photography and tensometric measurements, simulation of ventilated cavity bubbles near a free surface, experimental gas consumption and numerical predictions of cavity gas entrainment, simulation of liquid weightiness and free border effects, organization of the developed cavitation flow by supply of aqueous solutions of high-molecular linear-chain polymers. The numerical simulation results are compared with the proposed engineering solutions. The deficiencies of the available solutions are briefly discussed.